Good quality of air inhaled by the diver is a very important element not only for diving comfort, but also for diver safety. But what does good air quality mean and how do we define it?
Air is a mixture of mainly two gases oxygen (21%) and nitrogen (78%). In addition to this, air consists of other gases (1%) such as argon, carbon dioxide, neon, helium. From the point of view of diver safety, oxygen and carbon dioxide levels are important, and in addition, we want to detect elevated values of carbon monoxide, oil vapor and humidity.
The air quality standard most often referred to in diving is EN 12021, which talks about compressed gases for breathing apparatuses. It defines desirable and safe values for divers. Such air is not only very safe, but additionally meets the requirement of oxygen purity, which in practice guarantees the highest level of purity and quality of breathing air. The standard specifies maximum values for:
- Oxygen (21% +/- 1%) – oxygen is used to sustain life. Its insufficient content can cause a diver to lose consciousness due to hypoxia. It is a very rare situation for this parameter to be below the assumed values. The most common situation is when there is too much oxygen due to confusion and improper labeling of air and nitrox cylinders.
- Carbon dioxide (less than 0.05% / 500 ppm) – carbon dioxide is produced by the consumption of oxygen in the body’s metabolic processes. Among other things, its level in the human body controls the speed of breathing, so an increased value can cause breathing to speed up and become shallower. At depth, combined with increased gas density, this can cause major problems for divers such as feeling unable to take a full inhalation or increased impacts of gas narcosis. As a result, the diver may also experience more fatigue and headaches after the dive. Elevated levels of carbon dioxide in the intake air may be due to the quality of the air sucked into the compressor (e.g. In the industrial districts of cities, most often carbon dioxide levels are higher and may even exceed the normally permitted values. It is worth mentioning that the real risk to the diver begins when this standard is exceeded at least several times.
- Carbon monoxide (less than 0.0005% / 5 ppm) – carbon monoxide (commonly known as Chad) is a product of incomplete combustion, and its elevated content poses a real risk to divers. Since the gas is administered to the diver under pressure, its physiological effect will increase as the dive depth increases. This means that the safe values in the air breathed at depth can lead to poisoning of the diver at depth. Carbon monoxide in the air used by divers can come from exhaust fumes sucked into the compressor (e.g., from a car engine running next to the compressor’s air intake or exhaust fumes in compressors powered by an internal combustion engine) or an overheating compressor (burning oil due to excessive operating temperatures and, most often, old oil). Its presence is very dangerous and can even cause unconsciousness underwater or severe poisoning requiring post-dive treatment. To prevent this, a number of preventive mechanisms are used to prevent carbon monoxide from entering the mixture, as well as filter components that neutralize the aspirated carbon monoxide. For the recreational diving industry, however, this parameter is very rarely measured at the stage of filling or dispensing dive cylinders.
- Hydrocarbons / oils (less than 5mg /m3) – most compressors used in the recreational diving industry are lubricated with oil. In the process of teasing, a small amount of oil, or hydrocarbons, can get into the compressed air. The role of the filters is to catch these small amounts of hydrocarbons. If the permissible filter time is exceeded or the compressor malfunctions, elevated hydrocarbons may enter the compressed air. Their presence usually does not cause life-threatening or health-threatening symptoms, but they definitely reduce the comfort of breathing compressed air. In addition to measuring devices, smell can help detect hydrocarbon content (especially in people who are sensitive to the smell). However, the presence of an oil smell in the mixture does not mean that the air contains elevated hydrocarbon content. The presence of hydrocarbons in the mixture can also mean elevated levels of carbon monoxide also important to approach such air with great caution. It is best for safety not to use such air, or if you suspect the presence of hydrocarbons in the mixture you have already used to measure the carbon monoxide in the cylinder.
- Water content / water vapor / humidity (below 50 mg/m3) – too high a water content in the compressed air poses a risk of flooding of the automat during the dive. In the process of gas expansion, the breathing machine has a negative temperature, so the presence of water in the mixing is undesirable. Therefore, in the process of filling the cylinders, maximum air dehumidification is sought through multi-stage filtration. However, the filling of cylinders in a very humid environment combined with filter wear can lead to more water entering the cylinder. Moisture in the air can come from storing unscrewed cylinders in a humid environment.
How then to ensure the safety of the air used by divers. It is a multi-step process, each element of which plays an important role in enhancing the guarantee of good air quality. I will illustrate this with the example of Deepspot.
- Compressors / compressors – today, most modern compressors provide, when used properly, to meet the parameters described above. At Deepspot, we use 2 highly efficient electric MCH45 compressors from Coltri for air intake, and a combination of an LP300 nitrox diaphragm and an MCH18 compressor. All compressors are additionally equipped with desuperheaters, which improve the parameters of the air compressed by the compressors by lowering its temperature. By using electric compressor motors, we also avoid the risk of sucking carbon monoxide from the exhaust pipe of the compressor motor
- Regular servicing – each compressor requires periodic replacement of the filter set and oil. At Deepspot, trained technicians perform these exchanges in person and they are confirmed by keeping the appropriate records. In addition, all compressor service actions are performed by or under the supervision of Coltri personnel. This makes sure that the technical condition of the compressors and filters is good.
- Compressor operating conditions – compressors need a constant working environment for optimal operation. Compressors are particularly badly affected by elevated temperatures and lack of ventilation. At Deepspot, the compressors have an ideal working environment thanks to a dedicated room where we manage to maintain a temperature of 18-22C for most of the year even with the compressors running. In addition, the room is equipped with an automatic ventilation system. The air for the compressors is drawn in from the outside, and the intake is placed at a height of 2.5 meters to minimize the risk of fumes getting there.
- Internal testing – compressors can be equipped with various systems for monitoring air quality and the correctness of filters. For Deepspot, the MCH45 compressors are equipped with the PRESEC system, which monitors the condition of the air filters for their efficiency in trapping moisture and hydrocarbons. Together with regular filter changes, this ensures confirmation of proper operation of the main compressor filters. In addition, we have added air testing for the most safety-relevant parameter, namely the content (or lack thereof) of carbon monoxide. For this we use a carbon monoxide analyzer from De-OX connected to the cylinder filling system.
- Daily maintenance of compressors – In addition to maintenance activities, daily maintenance of compressors by Deepspot personnel ensures multiple daily checks of critical parameters such as filter operation, proper oil level and operating temperature.
- Cylinder cleanliness / cylinder contents – to ensure that the diver is breathing safe air, in addition to compressors, the condition of the cylinders should also be checked. At Deepspot, we do not refill our cylinders outside the center to guarantee the quality of the air entering the cylinder. In addition, the cylinders are regularly visually inspected in batches, and their cleanliness inside confirms that the systems described above are working properly. When cylinders are filled with damp and contaminated air, rust forms inside and oil can build up.
- External testing – advanced air analysis systems can be used to confirm the operation of the above systems. The most common way to do this is to use external auditors who have the right equipment, qualifications and certification capabilities. In the case of Deepspot, an external company conducts compressor air audits and Deepspot. Each time this is confirmed by the issuance of a certificate of air compliance with the PN-EN12021 standard described at the beginning of this article.
In summary, providing safe air is a complex process, and its complication increases with the size of the diving operation. The larger the scale, the more realistic elements of the system we should introduce and regularly inspect. At Deepsopot, we supply tens of thousands of cylinders of safe air and nitrox to divers and our staff each year. Based on this experience, we have refined a system that guarantees the quality and safety of the breathing mixtures used in our facility.
If you would have any questions about Deepspot systems, please feel free to contact us at: [email protected].
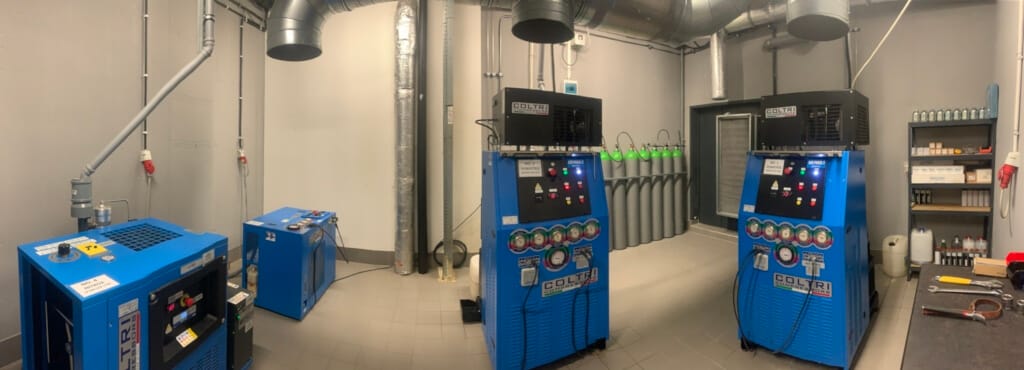
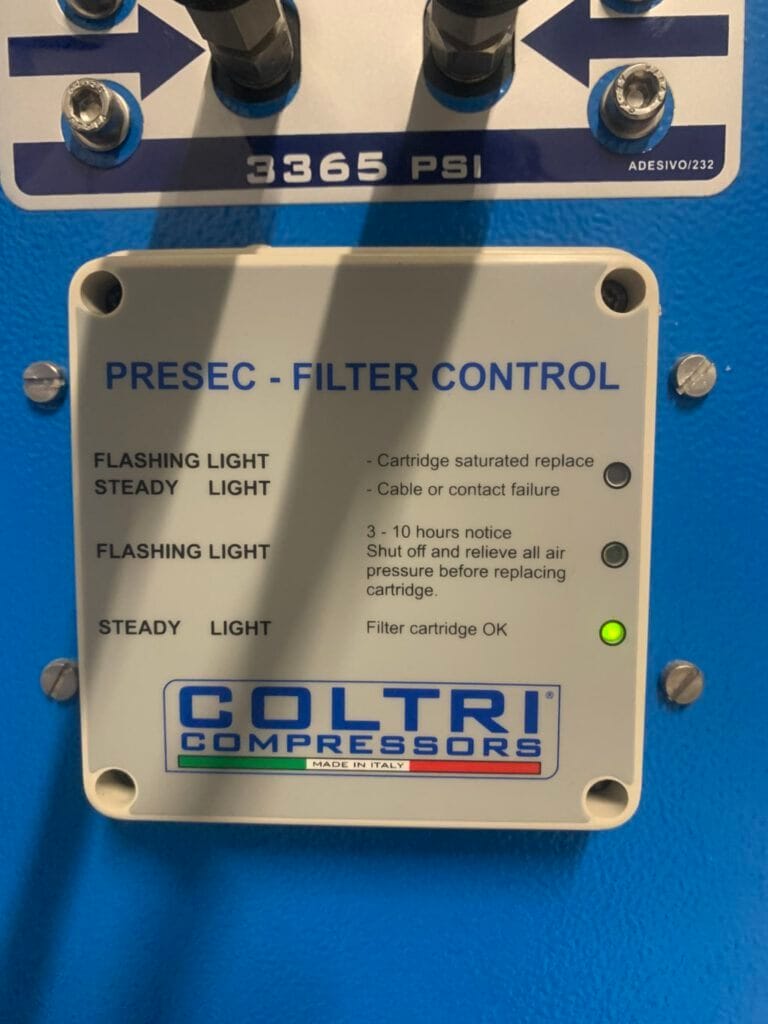
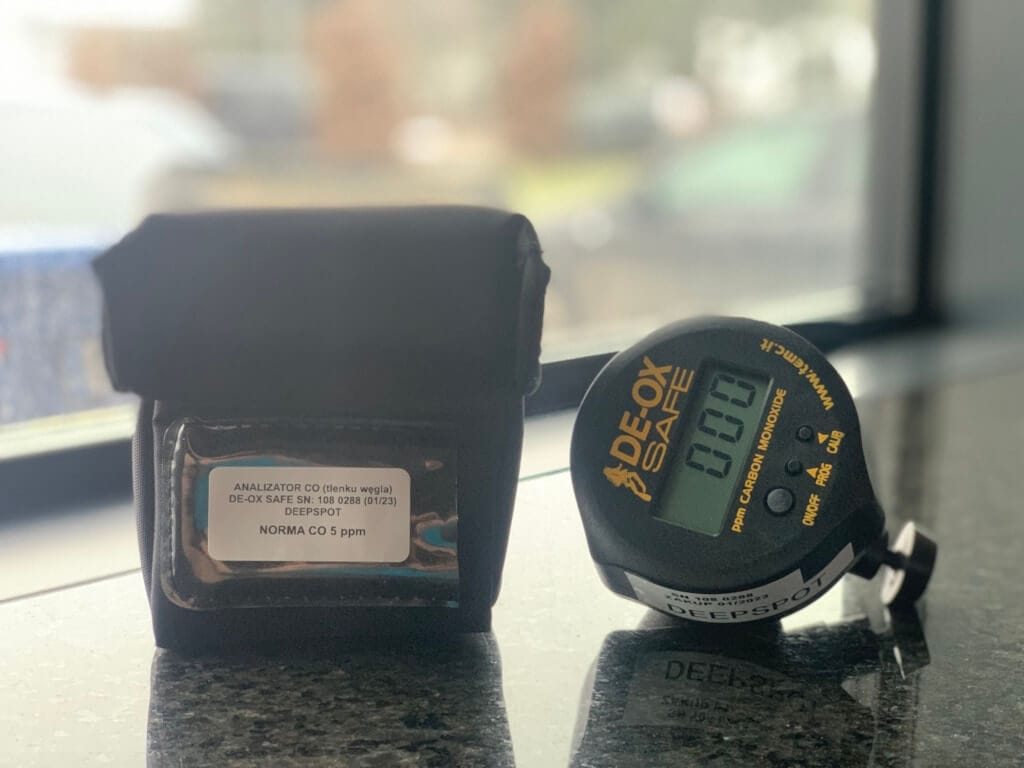
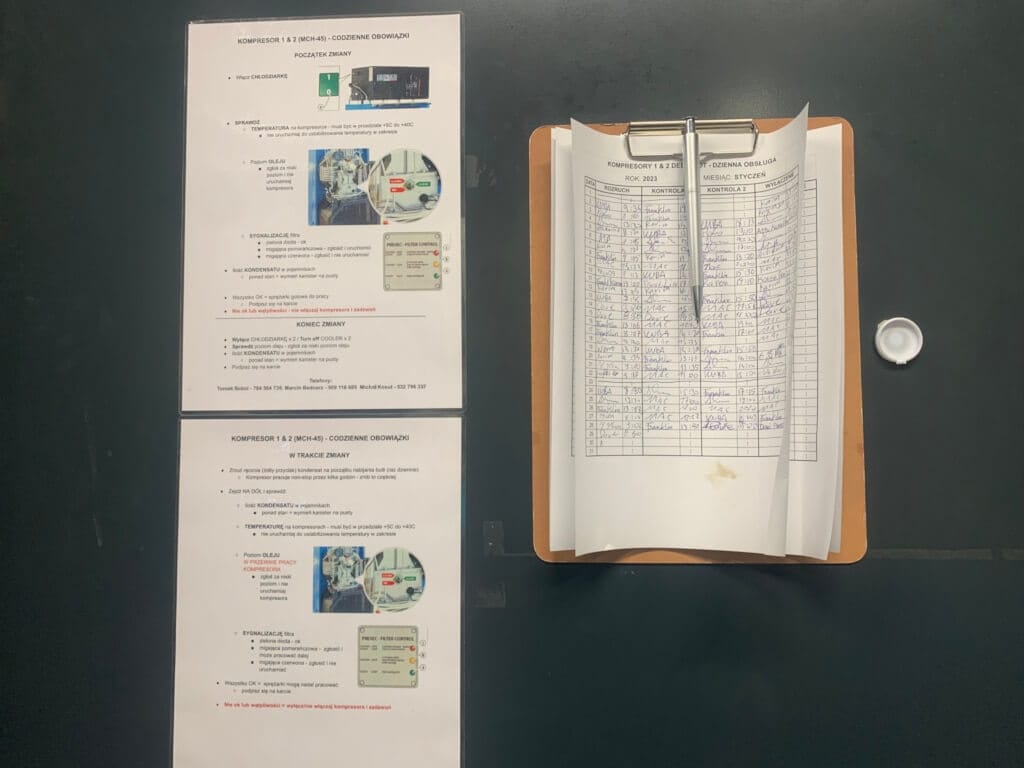